JarlBalgruuf
New Member
- Joined
- Nov 18, 2016
So I have spent the past 2 weeks making a custom waterblock for my GPU since only one company makes one and is asking $200 for it. (Zotac GTX 980 ti Amp extreme) . I milled out the copper and acrylic and made the block. The highest temp ive ever gotten with my air cooler is 71 C after hours of playing BF1. After I mounted my waterblock and got the loop all running, I booted my PC and launched BF1, I immediately noticed that my idle temps were around 40 C, as compared to my Air coolers 28-30 C. Within 5 minutes of playing BF1 I was up to 73 C. (Highest temp ive seen yet). Why is it that my watercooling is not working as it should?. Things ive checked: Fan is pulling air out of radiator, not blowing in. I am getting good flow through the waterblock. The thermal paste was applied correctly and the waterblock is mounted correctly, just as the stock cooler.
The only thing I can think of is the air bubbles, Ive bled it out 3 times and there are still a few little bubbles in the block. Does anyone have any idea what my problem might be? And do air bubbles really impact temps that extremely?
Note: The pictures were taken right after took the block off because I saw the higher temps.
The only thing I can think of is the air bubbles, Ive bled it out 3 times and there are still a few little bubbles in the block. Does anyone have any idea what my problem might be? And do air bubbles really impact temps that extremely?
Note: The pictures were taken right after took the block off because I saw the higher temps.
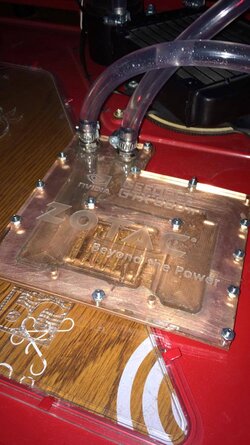
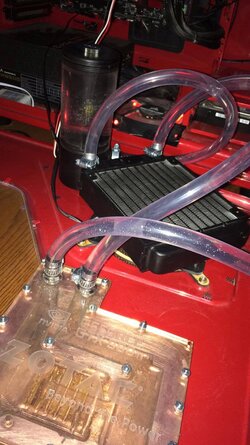