- Joined
- Dec 7, 2003
Project Vitis
Hi all,
I'm kicking off the thread for my latest project, tentatively titles Project Vitis.
My wife is currently using my old project, Jewel Box, but wanted a new case designed specifically for her.
She had a general theme in mind--a vine and leaf motif, as in the picture above (from http://www.clipartoday.com/clipart/nature/grassandtree/vine_308268.html).
Hence the title of this project, Vitis, which is the species name for vines (ie grape vines).
We kicked about general design and settled on a case roughly in size and build of my most recent project, Resilience (also known as the R unit during its building phase).
She was not interested in the curvy front panel of my Resilience box, so instead we decided to simplify it into a simple curved corner box a la mailbox or refrigerator.
I decided to do a little basic SketchUp to get a feel for the overall shape:
The primary shape was based on this simple profile:
A simple upright rectangle with rounded corners (3cm radius bends).
The general shape was going look like this:
Once again, the internal structure was going to be made from 1/2" MDF sheets, with virtually the same configuration as Resilience:
The surfaces would be made from 1/8" sheet acrylic. My wife specifically did NOT want the clear tinted plastic, so instead we opted for opaque plastic.
A little more on the aesthetic details.
We decided to have the side panels be glossy black.
The front, top and back face panels would all be white.
To incorporate the vine and leaf motif, the large front and back face panels would have the vine and leaf motif, like this ghetto SketchUp attempt:
The panel would be white, the vine and leaf pattern would actually be a cut-out from this surface panel, revealing an underneath purple plastic layer
Forgive my awful photoshopping skills, but it would look a little more like:
Finally, from a design aspect, I wanted to take all I had learned from my very prolonged Resilience project, and simplify. I wanted the case and the build process streamlined. And with the potential for future reproductions. I'm hoping to complete this project in 2-3 months.
.
Hi all,
I'm kicking off the thread for my latest project, tentatively titles Project Vitis.
My wife is currently using my old project, Jewel Box, but wanted a new case designed specifically for her.
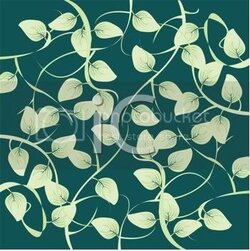
She had a general theme in mind--a vine and leaf motif, as in the picture above (from http://www.clipartoday.com/clipart/nature/grassandtree/vine_308268.html).
Hence the title of this project, Vitis, which is the species name for vines (ie grape vines).
We kicked about general design and settled on a case roughly in size and build of my most recent project, Resilience (also known as the R unit during its building phase).
She was not interested in the curvy front panel of my Resilience box, so instead we decided to simplify it into a simple curved corner box a la mailbox or refrigerator.
I decided to do a little basic SketchUp to get a feel for the overall shape:
The primary shape was based on this simple profile:
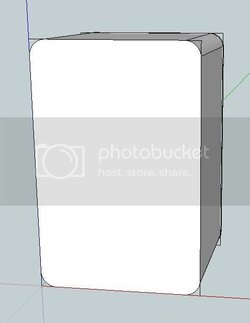
A simple upright rectangle with rounded corners (3cm radius bends).
The general shape was going look like this:
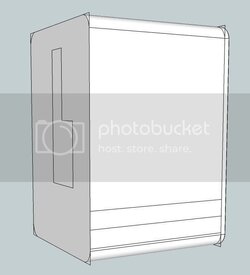
Once again, the internal structure was going to be made from 1/2" MDF sheets, with virtually the same configuration as Resilience:
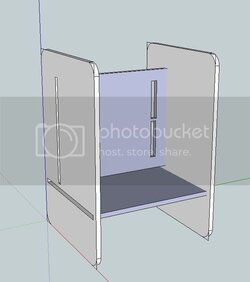
The surfaces would be made from 1/8" sheet acrylic. My wife specifically did NOT want the clear tinted plastic, so instead we opted for opaque plastic.
A little more on the aesthetic details.
We decided to have the side panels be glossy black.
The front, top and back face panels would all be white.
To incorporate the vine and leaf motif, the large front and back face panels would have the vine and leaf motif, like this ghetto SketchUp attempt:
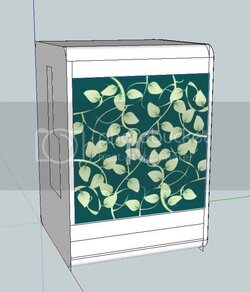
The panel would be white, the vine and leaf pattern would actually be a cut-out from this surface panel, revealing an underneath purple plastic layer
Forgive my awful photoshopping skills, but it would look a little more like:
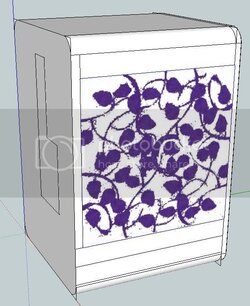
Finally, from a design aspect, I wanted to take all I had learned from my very prolonged Resilience project, and simplify. I wanted the case and the build process streamlined. And with the potential for future reproductions. I'm hoping to complete this project in 2-3 months.
.