- Joined
- Dec 5, 2001
- Location
- Canuckistan
I wanted to make this thread to discuss more the science of heat pipes, and especially so a major weakness that im starting to see with heatsinks that rely on heatpipes to transfer heat from the IHS.
From what i've read of bits and pieces about heat pipe design, is that they have an immense capacity to transfer heat even when there is not a very large difference in temperature. In this way, heat pipes can keep something much closer to ambient than a traditional block of metal with fins attached style heatsink. There is also a weakness in heat pipes. They must be calibrated for a temperature range. At some point within that range, there will be an optimal amount of heat transfer, as you move away from that point the heat transfer capacity will degrade. As temperatures increase, and the transfer capacity decreases, you reach a point, where the capacity to transfer heat has fallen to a level where it can just keep up with the heat being produced at the source. Once you go over this limit, the heat capacity falls, the temperature rises more, and you enter a downward spiral where the only amount of heat being transfered is done by the copper tubing itself, which offers about 1-2% of the original heat trasfer capacity.
Of course this is all mostly the way i see the science behind heat pipes, and i could be totally wrong. In order to elaborate a bit, i'll explain what understand of heat pipes.
The basic design of a heat pipe is simple. The pipe itself is any normal piece of pipe, that has a modified inside surface. The pipe is vacuum sealed and filled with a tiny amount of liquid. The vacuum sealing provides a low-pressure environment, allowing the liquid to evaporate into a gas at a much lower temperature then it would at normal atmospheric pressure. The modified inside surface of the pipe is designed to allow what is called capillarity, or 'wicking'.
When one end of a heat pipe is exposed to a heat source, the liquid in that area evaporates, absorbing heat. This increase in evaporation also increases the pressure in this area causing the vapor to move to the colder area where there is less pressure. As it does this it begins to cool, and eventually condensates, releasing the heat, on the inside wall of the pipe. Because of the design of the inside of the pipe, the water wicks its way back towards the heat source until it reaches a zone that is warm enough for it to evaporate again, repeating the cycle.
In an optimal setup, the liquid makes its way back, or at least relatively close, to the heat source and continues transferring heat from the source to the colder area of the pipe. As the temperature increases at the heat source, the point at which evaporation happens begins to move further away from the heat source. The further the point of evaporation occurs from the heat source, the less heat transfer capacity the heat pipe has, thus causing the heat source to attain higher temperatures.
To give an example of this, here's two graphs of a heatsink im using that relies 100% on heat pipes to transfer heat to a fin array.
This graph is my system, a Phenom 9850 running at 2875Mhz at stock 1.3v. As you can see my idle temps are quite low, and my load temps are quite good also.
Now here's what happens to those load temps when i increase only the voltage to 1.3375v.
In the second graph, there are multiple places where the temperature begins to plateau, and almost stabilize before jumping up to a new level. At around 52c, it breaks through and starts to rise dramatically. Had i not stopped Prime95 from running, those temperatures would have continued until my system crashed or my chip fried. To give you an example of an extreme situation i encountered...
This was the first time i had installed this heatsink. The overclock i had at the time was around 3.1ghz with 1.45v. My stock AMD heatsink was having stable load temps in the low 60c range. That heatsink is a more traditional design, fins attached to a block, that also has heatpipes running from the base into the fins to help. But it does not rely on heat pipes.
Now, im not a scientist, nor an expert, im just a man who loves his science and especially thermodynamics. So i could be completely wrong about some of the observations i've made and my interpretation of the data. But i would like to know if anyone else has seen similar results with heatsink designs that rely on the thermal capacity of heat pipes. And even better, if you happen to be a thermodynamics expert, possibly enlighten me towards some misconceptions i have about the design and operation of heat pipes.
From what i've read of bits and pieces about heat pipe design, is that they have an immense capacity to transfer heat even when there is not a very large difference in temperature. In this way, heat pipes can keep something much closer to ambient than a traditional block of metal with fins attached style heatsink. There is also a weakness in heat pipes. They must be calibrated for a temperature range. At some point within that range, there will be an optimal amount of heat transfer, as you move away from that point the heat transfer capacity will degrade. As temperatures increase, and the transfer capacity decreases, you reach a point, where the capacity to transfer heat has fallen to a level where it can just keep up with the heat being produced at the source. Once you go over this limit, the heat capacity falls, the temperature rises more, and you enter a downward spiral where the only amount of heat being transfered is done by the copper tubing itself, which offers about 1-2% of the original heat trasfer capacity.
Of course this is all mostly the way i see the science behind heat pipes, and i could be totally wrong. In order to elaborate a bit, i'll explain what understand of heat pipes.
The basic design of a heat pipe is simple. The pipe itself is any normal piece of pipe, that has a modified inside surface. The pipe is vacuum sealed and filled with a tiny amount of liquid. The vacuum sealing provides a low-pressure environment, allowing the liquid to evaporate into a gas at a much lower temperature then it would at normal atmospheric pressure. The modified inside surface of the pipe is designed to allow what is called capillarity, or 'wicking'.
When one end of a heat pipe is exposed to a heat source, the liquid in that area evaporates, absorbing heat. This increase in evaporation also increases the pressure in this area causing the vapor to move to the colder area where there is less pressure. As it does this it begins to cool, and eventually condensates, releasing the heat, on the inside wall of the pipe. Because of the design of the inside of the pipe, the water wicks its way back towards the heat source until it reaches a zone that is warm enough for it to evaporate again, repeating the cycle.
In an optimal setup, the liquid makes its way back, or at least relatively close, to the heat source and continues transferring heat from the source to the colder area of the pipe. As the temperature increases at the heat source, the point at which evaporation happens begins to move further away from the heat source. The further the point of evaporation occurs from the heat source, the less heat transfer capacity the heat pipe has, thus causing the heat source to attain higher temperatures.
To give an example of this, here's two graphs of a heatsink im using that relies 100% on heat pipes to transfer heat to a fin array.
This graph is my system, a Phenom 9850 running at 2875Mhz at stock 1.3v. As you can see my idle temps are quite low, and my load temps are quite good also.
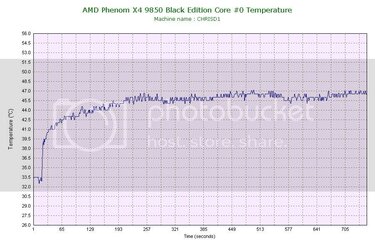
Now here's what happens to those load temps when i increase only the voltage to 1.3375v.
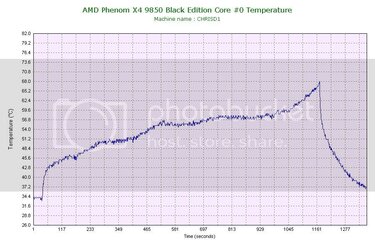
In the second graph, there are multiple places where the temperature begins to plateau, and almost stabilize before jumping up to a new level. At around 52c, it breaks through and starts to rise dramatically. Had i not stopped Prime95 from running, those temperatures would have continued until my system crashed or my chip fried. To give you an example of an extreme situation i encountered...
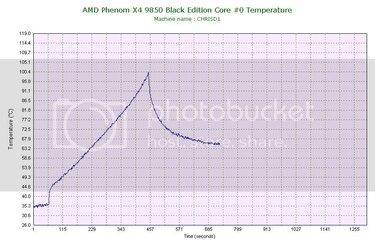
This was the first time i had installed this heatsink. The overclock i had at the time was around 3.1ghz with 1.45v. My stock AMD heatsink was having stable load temps in the low 60c range. That heatsink is a more traditional design, fins attached to a block, that also has heatpipes running from the base into the fins to help. But it does not rely on heat pipes.
Now, im not a scientist, nor an expert, im just a man who loves his science and especially thermodynamics. So i could be completely wrong about some of the observations i've made and my interpretation of the data. But i would like to know if anyone else has seen similar results with heatsink designs that rely on the thermal capacity of heat pipes. And even better, if you happen to be a thermodynamics expert, possibly enlighten me towards some misconceptions i have about the design and operation of heat pipes.