I don't often post, but I've been lurking on these forums for awhile using all the sage advice -- or at least reading it and still ignoring it
Fair warning.. I'm verbose but hopefully not boring.
Not that my build is anything people haven't seen before, but I thought that maybe by reading my mistakes and the fun I had others may avoid them -- or step into them with both feet anyways!
Quick background:
For the last 5 years or so I've been interested in the mITX form factor and cases such as the InWin 901 and Phanteks Evolv Shift. Both cases were great -- though the 901 was a pain to work in much moreso that than the Shift.
I then hopped onboard the AOI train when those started coming to market. They were OK -- but really, all it did was cram a few hard to bend and ugly tubes into my small cases. All was well however and I liked having a small case hidden away under my desk.
Then -- I got bored and was really getting annoyed with reading about features on the ATX boards these days -- as well as the general PIA of working in those small cases -- I decided to walk back into the world of ATX cases and MB's.
Since I was going to have this monster case lurking on my desk now, I thought let's just go a step further and throw a custom loop into the mix. That was pretty easy and straightforward, bought an EK 240 Extreme kit at Microcenter and popped in -- no problemo.
Thing is.. it looked kinda like garbage. I'm not one to really care about that too much, but I do like things looking nice and tidy if I can make it happen. So with all these plastic tubes running around, what was I to do? Of course! PETG or glass would clean things up!
PETG seemed pretty simple and easy to work with, but the borosicilicate glass seemed like a good challange with far less information available to learn from (though everything you need is out there -- just gotta dig a bit and infer a lot). I like a challange.
I ended up going with Mayhems 13mm glass. I went with Mayhems based on the couple of reviews I could find -- they also offered 90 bends which meant 1) less connectors which are pricey and 2) It would look nice and tidy. I bought 6 straight tubes and 6 with 90 bends in them.
Next up fittings: Lucky for me (depending on your view of choices) I had no choice as only Alphacool made compression fittings for hard tubing in 13mm. Perfect!
Now I had the glass, what else..
Seemed like I was good to go.
Day 1:
Let's do this. Drained the existing distilled water and ripped out all the plastic tubing. First issue already. I'm an idiot and ended up dumping loads of water directly into the power supply.. Great.. So i spend the next hour or so taking that a part and sucking up all water with about 1,000 qtips. With the PSU dry and put back together it's time to carry on. No harm no foul.
I tried to do a few test fittings to get the feel for how much pressure is needed to push the glass tubes into the fittings. I used the only option available for 13mm glass, the Alphacool 13mm compression fittings. Because I'm daft, i just kept trying to jam the tubes into the fittings -- using all of my might and the thing just fall right out.. What the hell? I did this for probably an hour or two thinking the fittings were bad or I bought the wrong ones. Lubing them up with water. I even pushed so hard I shattered two tubes directly into my hands -- fun times
Now I'm getting frustrated -- my back is sore from standing at the counter all day -- and I just want to play a damn video game at this point. So i suck it up and just shove all the plastic tubing back on -- I don't even bother with putting the compression tops back on.. just go the F on and let me be done. Basically day 1 was a disaster and ended where I started but with broken tubes and a few bloody fingers.
A few days later:
I cannot shake the feeling I'm doing something wrong -- I'm pretty mechanically inclined -- but obviously not particularly patient. I watched several videos on glass tube cutting and such and it NEVER dawned on my why those chamfers are so important. Dumb as I am, I had chamfers the ends after cutting, but not well.
I took another a small piece of glass I cut earlier with the Dremel diamond wheel (works very well!!), and decided to use that to crate the chamfers rather than needle files. This worked like a charm. Set the Dremel to low speed when cutting (1,000 -1,500 rpm abouts) and then ramp that thing up to 2,500 when sanding the tip and creating the chamfers. So freaking easy.
Of course that made all the difference and I'm pretty sure I squeeled like a schoolgirl the first time a tube popped into the fitting securely with relatively little pressure. I had figured out where I went wrong and could now get this thing back on track soon.
A further few days later:
I felt good. I could chamfer like a champ. I start off cutting a few pieces, all is well. I'm putting things together in the case and pushing the tubing in -- and realize.. umm, these are not aligning on one plane or another with the next fitting. What do I do now? This is glass, I know. But for some reason my brain could not control the urge to just make it fit. So of course i just try to bend it slightly to align and.. SNAP.. broken.
I'm now thinking this all futile and a waste of time and money. I should just go back to the crappy soft plastic ugly tubing and stfu. I'll lost. Done. Finito.
Even more days later:
I cannot stop thinking about being defeated by stupid glass tubing.. I mean, c'mon! I've torn down and repaired my entire HVAC system, fixed/replaced burst pipes in the walls, and all sorts of other home stuff, this was peanuts. So i start reading again and looking at forums here and there for build logs.
The general concensius was that it's probably smart of do this with PETG first then cut your glass tubes to the right size based on the PETG setup. OK, no problem. So i buy some cheap PETG tubing to use as guides. I've got loads of pipe cutting tools around so no need to buy any kits or anything. Copper pipe cutters work well on this -- or at least for me it worked fine. I wasn't going to bother with a heat gun to bend the PETG since I just wanted to use the tubes as guides for the lenght of glass I needed.
Cool here we go.. wait, do you remember how thigns weren't aligning and I broke the glass tube trying to flex it (I still laugh at how stupid that was)? No? Me eiither and here I sat with no 45 degree or rotary fittings.
I realize that is what I need to make this work -- so I buy some 45 rotary and 90 rotary fittings. I already had a few elbows laying around, but needed more flexability.
In the meantime I thought I'd put the new EK Glacier rez in and see how that looked and fit. I took the op off my pump and mounted it to the rez as per the instructions. Now I'm using the pump from the EK Kit --- a DDC pump with aluminum heatsink (I could not remove the heatsink it seemed and really didn't want to break it trying to rip it off). I mounted the pump and put some tap water in the rez over the sink to test the fitting. It leaked immediately and I could see gap between the pump and the acrylic of the rez. Okay. I'll tighten it. And... CRACK. I drove a screw straight through the acrlyic and broke the rez for good. There goes another another $100+. I'm a moron. I put the old rez back in, cursed, and went to the bar to drown my sorrows.
Next shot:
Now I have the fittings I think I need, PETG tubing, glass tubing, and all the appropriate hardware. It's Sunday and I'm for damn sure getting this done TODAY!
I decided to make myself comfortable rather than standing at a kitchen counter. I waas going to be an all day afair. I setup on the coach and coffee table in the morning ready to watch Wimbledon finals, the World Cup finals, and a few movies. I pull out the exiting loop and stare for awhile thinking about how to do this properly. I WILL TAKE MY TIME!
I start looking and measure the PETG and just can't handle doing the same thing twice. I was going to take my time, but not with the PETG. So I'm just gonna go for it once more and cut the glass without using PETG as a guide. Plus I bought 16mm PETG and had no fittings that fit so I'd have to try and tape that crap into place which wouldn't be effective or accurate.
Here is the thing... I just took my time with the glass instead of spending it on the PETG. Cut things long, sanded, chamfered. Cut a bit shorter, sanded, chamfered.. and on and on and on until the piece fit the run I needed it to. This was made very easy by using the Dremel diamond wheel for everything. WORD OF CAUTION: This thing puts out so much silica dust -- you MUST wear a mask or you will be inhaling this stuff which is extremely hazardous to your lungs. I did this in my garage of course -- not on my couch.
So over the course of Wimbledon finals, World Cup finals, and two movies later -- I had cut all the tubes and actually had them in place and fitting together nicely. I had one major scare here with the last run of tube from the GPU back to the res. It was a longer run and I had only two compression fittings left... so I couldn't muck about with extra fittings in the run and had to do it with two.
By this stage, after all my screws ups, etc.. I had one lengthy piece of glass left with a 90 degree bend it. I had one chance. And the evening news was coming on, so I'm starting to realize I'd like to wrap this up very soon..
That said, I've probaby never done something so slowly and carefully because if I screwed this piece up -- i was dead in the water until I could get more glass shipped. That or I'd have to have a long run of flimsy plastic tubing -- and that was not gonna happen!
Luckily enough -- I was able to get it to fit. I was relieved as it was my last chance.
Final Steps:
Time to fill this thing up and let it roll. I had some Mayhems Blue Pastel around (dyes... I know I know..) I decided to use this as it'd would be so easy to spot leaks by eye or with a paper towel. I also like the look of it and realize I'll be cleaning my parts at some point (or more realistically, I'll replace them on a whim). To my chagrin I had two very small leaks that were taken care of with a bit of tighening of the fittings. Drops came out, not a flood of coolant -- no biggie.
As of this morning there are no leaks and things are running smoothly. I could lie and say I'm typing on another machine while the last 12 hours of the leak test wrap up, and I probably should be -- but of course I am not and am taking a risk. So far so good.
This is a very long read and I apologize for that. Hoping it was at least informative and not completely mind numbing to read. If anything however, I hope at least one person has learned the following:
READ EVERYTHING YOU CAN MORE THAN ONCE, MEASURE TWICE CUT ONCE, CUT LONG AND CUT AGAIN, MAP OUT YOUR BUILD WITH EVERY SINGLE FITTING YOU NEED and most of all.. TAKE YOUR TIME -- IT WILL SAVE YOU IN THE LONG RUN!
If you think you're going to wing it one afternoon -- you might.. or you might spend a week and a lot of extra money that isn't needed
All in all -- I had a lot of fun -- learned a lot which is the best part, and am already excited to do it again in a year or so. Or, probably sooner because it's fun to tinker. I'm already thinking of setting up a little workshop to bend this glass to my whim -- I look forwad to the battle once more.
Here is a crappy picture to show what I've done. I still need to clean-up a few things. Cable combs, fingerprints on the glass, the backplate of the gpu.. etc..
Not that my build is anything people haven't seen before, but I thought that maybe by reading my mistakes and the fun I had others may avoid them -- or step into them with both feet anyways!
Quick background:
For the last 5 years or so I've been interested in the mITX form factor and cases such as the InWin 901 and Phanteks Evolv Shift. Both cases were great -- though the 901 was a pain to work in much moreso that than the Shift.
I then hopped onboard the AOI train when those started coming to market. They were OK -- but really, all it did was cram a few hard to bend and ugly tubes into my small cases. All was well however and I liked having a small case hidden away under my desk.
Then -- I got bored and was really getting annoyed with reading about features on the ATX boards these days -- as well as the general PIA of working in those small cases -- I decided to walk back into the world of ATX cases and MB's.
Since I was going to have this monster case lurking on my desk now, I thought let's just go a step further and throw a custom loop into the mix. That was pretty easy and straightforward, bought an EK 240 Extreme kit at Microcenter and popped in -- no problemo.
Thing is.. it looked kinda like garbage. I'm not one to really care about that too much, but I do like things looking nice and tidy if I can make it happen. So with all these plastic tubes running around, what was I to do? Of course! PETG or glass would clean things up!
PETG seemed pretty simple and easy to work with, but the borosicilicate glass seemed like a good challange with far less information available to learn from (though everything you need is out there -- just gotta dig a bit and infer a lot). I like a challange.
I ended up going with Mayhems 13mm glass. I went with Mayhems based on the couple of reviews I could find -- they also offered 90 bends which meant 1) less connectors which are pricey and 2) It would look nice and tidy. I bought 6 straight tubes and 6 with 90 bends in them.
Next up fittings: Lucky for me (depending on your view of choices) I had no choice as only Alphacool made compression fittings for hard tubing in 13mm. Perfect!
Now I had the glass, what else..
- I already had the res and pump from the EK kit.
- I had a radiator from the kit but it was a massive thing (double wide?) -- and really took a load of space in the front of the case forcing me to mount the res towards the back. Not ideal.
- A diamond Dremel wheel and diamond needle files for sanding/cutting.
- EK Glacier Res -- I literally bought this on looks alone.. sue me.
- 1080ti waterblock (2 of them, because the stupid DVI port on my EVGA SC Black Edition isn't on the reference board.. Of course I didn't notice till ripped it apart and used the thermal pads. Loss of a $100+ on that.
- Two new radiators:
- Hardware labs Black Ice 360GTS (top)
- Hardware labs Black Ice 240GTX (front) to replace the EK monster. It's not much smaller, but an inch is a mile sometimes.
Seemed like I was good to go.
Day 1:
Let's do this. Drained the existing distilled water and ripped out all the plastic tubing. First issue already. I'm an idiot and ended up dumping loads of water directly into the power supply.. Great.. So i spend the next hour or so taking that a part and sucking up all water with about 1,000 qtips. With the PSU dry and put back together it's time to carry on. No harm no foul.
I tried to do a few test fittings to get the feel for how much pressure is needed to push the glass tubes into the fittings. I used the only option available for 13mm glass, the Alphacool 13mm compression fittings. Because I'm daft, i just kept trying to jam the tubes into the fittings -- using all of my might and the thing just fall right out.. What the hell? I did this for probably an hour or two thinking the fittings were bad or I bought the wrong ones. Lubing them up with water. I even pushed so hard I shattered two tubes directly into my hands -- fun times
Now I'm getting frustrated -- my back is sore from standing at the counter all day -- and I just want to play a damn video game at this point. So i suck it up and just shove all the plastic tubing back on -- I don't even bother with putting the compression tops back on.. just go the F on and let me be done. Basically day 1 was a disaster and ended where I started but with broken tubes and a few bloody fingers.
A few days later:
I cannot shake the feeling I'm doing something wrong -- I'm pretty mechanically inclined -- but obviously not particularly patient. I watched several videos on glass tube cutting and such and it NEVER dawned on my why those chamfers are so important. Dumb as I am, I had chamfers the ends after cutting, but not well.
I took another a small piece of glass I cut earlier with the Dremel diamond wheel (works very well!!), and decided to use that to crate the chamfers rather than needle files. This worked like a charm. Set the Dremel to low speed when cutting (1,000 -1,500 rpm abouts) and then ramp that thing up to 2,500 when sanding the tip and creating the chamfers. So freaking easy.
Of course that made all the difference and I'm pretty sure I squeeled like a schoolgirl the first time a tube popped into the fitting securely with relatively little pressure. I had figured out where I went wrong and could now get this thing back on track soon.
A further few days later:
I felt good. I could chamfer like a champ. I start off cutting a few pieces, all is well. I'm putting things together in the case and pushing the tubing in -- and realize.. umm, these are not aligning on one plane or another with the next fitting. What do I do now? This is glass, I know. But for some reason my brain could not control the urge to just make it fit. So of course i just try to bend it slightly to align and.. SNAP.. broken.
I'm now thinking this all futile and a waste of time and money. I should just go back to the crappy soft plastic ugly tubing and stfu. I'll lost. Done. Finito.
Even more days later:
I cannot stop thinking about being defeated by stupid glass tubing.. I mean, c'mon! I've torn down and repaired my entire HVAC system, fixed/replaced burst pipes in the walls, and all sorts of other home stuff, this was peanuts. So i start reading again and looking at forums here and there for build logs.
The general concensius was that it's probably smart of do this with PETG first then cut your glass tubes to the right size based on the PETG setup. OK, no problem. So i buy some cheap PETG tubing to use as guides. I've got loads of pipe cutting tools around so no need to buy any kits or anything. Copper pipe cutters work well on this -- or at least for me it worked fine. I wasn't going to bother with a heat gun to bend the PETG since I just wanted to use the tubes as guides for the lenght of glass I needed.
Cool here we go.. wait, do you remember how thigns weren't aligning and I broke the glass tube trying to flex it (I still laugh at how stupid that was)? No? Me eiither and here I sat with no 45 degree or rotary fittings.
I realize that is what I need to make this work -- so I buy some 45 rotary and 90 rotary fittings. I already had a few elbows laying around, but needed more flexability.
In the meantime I thought I'd put the new EK Glacier rez in and see how that looked and fit. I took the op off my pump and mounted it to the rez as per the instructions. Now I'm using the pump from the EK Kit --- a DDC pump with aluminum heatsink (I could not remove the heatsink it seemed and really didn't want to break it trying to rip it off). I mounted the pump and put some tap water in the rez over the sink to test the fitting. It leaked immediately and I could see gap between the pump and the acrylic of the rez. Okay. I'll tighten it. And... CRACK. I drove a screw straight through the acrlyic and broke the rez for good. There goes another another $100+. I'm a moron. I put the old rez back in, cursed, and went to the bar to drown my sorrows.
Next shot:
Now I have the fittings I think I need, PETG tubing, glass tubing, and all the appropriate hardware. It's Sunday and I'm for damn sure getting this done TODAY!
I decided to make myself comfortable rather than standing at a kitchen counter. I waas going to be an all day afair. I setup on the coach and coffee table in the morning ready to watch Wimbledon finals, the World Cup finals, and a few movies. I pull out the exiting loop and stare for awhile thinking about how to do this properly. I WILL TAKE MY TIME!
I start looking and measure the PETG and just can't handle doing the same thing twice. I was going to take my time, but not with the PETG. So I'm just gonna go for it once more and cut the glass without using PETG as a guide. Plus I bought 16mm PETG and had no fittings that fit so I'd have to try and tape that crap into place which wouldn't be effective or accurate.
Here is the thing... I just took my time with the glass instead of spending it on the PETG. Cut things long, sanded, chamfered. Cut a bit shorter, sanded, chamfered.. and on and on and on until the piece fit the run I needed it to. This was made very easy by using the Dremel diamond wheel for everything. WORD OF CAUTION: This thing puts out so much silica dust -- you MUST wear a mask or you will be inhaling this stuff which is extremely hazardous to your lungs. I did this in my garage of course -- not on my couch.
So over the course of Wimbledon finals, World Cup finals, and two movies later -- I had cut all the tubes and actually had them in place and fitting together nicely. I had one major scare here with the last run of tube from the GPU back to the res. It was a longer run and I had only two compression fittings left... so I couldn't muck about with extra fittings in the run and had to do it with two.
By this stage, after all my screws ups, etc.. I had one lengthy piece of glass left with a 90 degree bend it. I had one chance. And the evening news was coming on, so I'm starting to realize I'd like to wrap this up very soon..
That said, I've probaby never done something so slowly and carefully because if I screwed this piece up -- i was dead in the water until I could get more glass shipped. That or I'd have to have a long run of flimsy plastic tubing -- and that was not gonna happen!
Luckily enough -- I was able to get it to fit. I was relieved as it was my last chance.
Final Steps:
Time to fill this thing up and let it roll. I had some Mayhems Blue Pastel around (dyes... I know I know..) I decided to use this as it'd would be so easy to spot leaks by eye or with a paper towel. I also like the look of it and realize I'll be cleaning my parts at some point (or more realistically, I'll replace them on a whim). To my chagrin I had two very small leaks that were taken care of with a bit of tighening of the fittings. Drops came out, not a flood of coolant -- no biggie.
As of this morning there are no leaks and things are running smoothly. I could lie and say I'm typing on another machine while the last 12 hours of the leak test wrap up, and I probably should be -- but of course I am not and am taking a risk. So far so good.
This is a very long read and I apologize for that. Hoping it was at least informative and not completely mind numbing to read. If anything however, I hope at least one person has learned the following:
READ EVERYTHING YOU CAN MORE THAN ONCE, MEASURE TWICE CUT ONCE, CUT LONG AND CUT AGAIN, MAP OUT YOUR BUILD WITH EVERY SINGLE FITTING YOU NEED and most of all.. TAKE YOUR TIME -- IT WILL SAVE YOU IN THE LONG RUN!
If you think you're going to wing it one afternoon -- you might.. or you might spend a week and a lot of extra money that isn't needed
All in all -- I had a lot of fun -- learned a lot which is the best part, and am already excited to do it again in a year or so. Or, probably sooner because it's fun to tinker. I'm already thinking of setting up a little workshop to bend this glass to my whim -- I look forwad to the battle once more.
Here is a crappy picture to show what I've done. I still need to clean-up a few things. Cable combs, fingerprints on the glass, the backplate of the gpu.. etc..
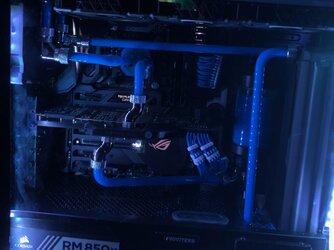