- Joined
- Dec 7, 2003
Exoframe 2.0
A few years back I built my Exoframe Project.
Build log is here.
Completed project thread is here.
I was recently contacted by GMdoubleG at the ocforums about possibly building a similar case. I told him that I could, but it would take a while because, as I mentioned in the original thread, I’ve always wanted to build stronger 3 way corner brackets from steel.
Well, I contacted some local NorCal guys, Erik at Norcal laser and Matt at Mione’s Solidworks, and after a few revisions, I had a steel 3 way corner bracket.
The thread on the design and fabrication of my 3 way corner brackets is here.
GMdoubleG had some specifics.
Looking for more of a cube shape. Horizontal motherboard. Two 2x120mm radiators up top.
Plan was to leave the aluminum bars and steel corner bracket unfinished--he would have a local painter powdercoat and/or anodize.
Going with all gray plastic paneling.
He passed along some general design drawings:
A few years back I built my Exoframe Project.
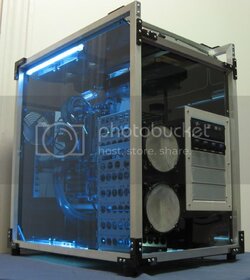
Build log is here.
Completed project thread is here.
I was recently contacted by GMdoubleG at the ocforums about possibly building a similar case. I told him that I could, but it would take a while because, as I mentioned in the original thread, I’ve always wanted to build stronger 3 way corner brackets from steel.
Well, I contacted some local NorCal guys, Erik at Norcal laser and Matt at Mione’s Solidworks, and after a few revisions, I had a steel 3 way corner bracket.
The thread on the design and fabrication of my 3 way corner brackets is here.
GMdoubleG had some specifics.
Looking for more of a cube shape. Horizontal motherboard. Two 2x120mm radiators up top.
Plan was to leave the aluminum bars and steel corner bracket unfinished--he would have a local painter powdercoat and/or anodize.
Going with all gray plastic paneling.
He passed along some general design drawings:
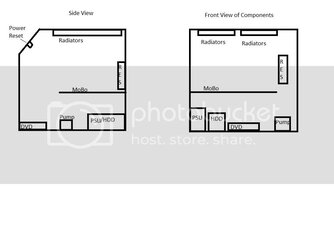
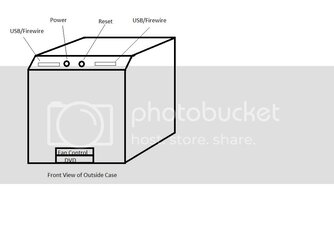
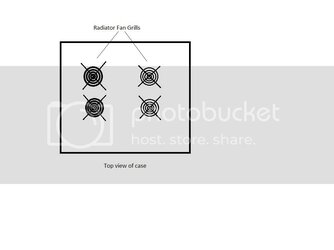