- Joined
- Dec 7, 2003
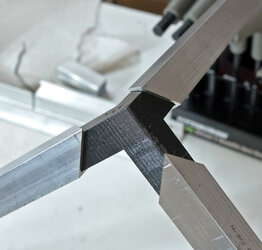
Exoframe 3D
This is the build log for my latest scratch built mod. It’s been a little while since my last post (Vertical Benching Station), due to life, and some health issues. Exoframe 3D is based on my previous concepts of an Exoframe--a chassis of square tube aluminum, with inset acrylic paneling.
The “3D” portion of the name may be a little confusing, as obviously the mod is 3 dimensional. “3D” refers to the incorporation of a new skill set to my modding:
a 3D printer!
Post magically merged:
Let me introduce you to my 3D printer:
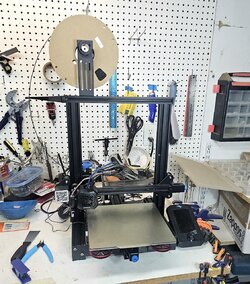
Bought off Amazon Prime Days, I picked up the Creality Ender 3 V2, the quintessential DIYer’s 3D printer. If you aren’t familiar with 3D printers, this is the general starter’s 3D printer for people who want to learn about 3D printing and be able to troubleshoot a printer. This is not the fully assembled bells and whistles ready to go out of the box printer.
So of course, here are my mods and upgrades:
Upgraded springs
Cable clips and filament holders
CR Touch auto bed-leveler
Flexible magnetic bed
Capricorn tubing
Filament sleeve mod
Generally, I've been using Inland black PLA.
Last edited: