- Joined
- May 8, 2011
- Location
- Darlington, South Carolina
- Thread Starter
- #21
Way, way out of line.
I was just asking a question.
I am just collecting data. How could you possibly see an attack from a mere question?
I have in one way or another been attacked from day one by various individuals for even considering chilled water cooling so for me it is an expected and common thing to happen. My response to you is in my opinion quite tame from my days of old here regarding my attitude, if you don't believe me ask EarthDog, you got the mild version! By the way the very character you chose for an Avatar was always experimenting to improve his inventions, well the fact that I am at version 4.0 and still experimenting, should tell you at least it did not start with this thread. So that's why your opinion does not matter to me it has no bearing on my experimentation.
That said post a link to your cooling and lets see what you run?
I've always been open, maybe you have a better idea, IDK, but if it is just conventional cooling, Been There Done That!
For my own data collection, I would love to see the following numbers:
1. Ambient temperature of the room wherein the chiller is being tested.
2. Average core temperature under full load.
3. Wattage being reported under full load.
That will give me enough information to rate your entire cooling solution.
#1 My ambient room temperature is usually 24c maintained and may vary .5 either way, but ambient room temperature is really irrelevant when you are using a negative DeltaT cooling, meaning 14c below ambient. Ambient does have an effect when it comes to condensation on the outside of the CPU cooling water block, but at a 10c coolant temperature there has been no condensation to be concerned with at all. I do not run motherboard moisture insulation and never have, I operate in a below ambient window, meaning below ambient, but above condensation forming temperatures. That said using traditional ambient calculations to measure efficiency of chilled water cooling is kinda a joke isn't it. Seeing as how it is an active cooling system wouldn't the amount of electrical power being used vs results be a better conclusion to rate a chilled water cooling solution. You must also calculate in the unknown variable, which is the 3rd TEC assembly controlled by the thermal controller that controls the 10c coolant window, meaning the 3rd TEC is not powered all the time, only when needed. That 10c coolant window is cut in at 11c cut out at 9.9c to maintain a 10c operational window. Which is cut in power at 11.0c, active temperature drop, 10.9, 10.8, 10.7, 10.6, 10.5, 10.4, 10.3, 10.2 10.1, 10.0, 9.9c cut out power, which is the 10c operational window and the missing information is the time variable from cut in and cut out. So there are more factors to calculate into the equation besides ambient room temperature.
You can get #2 and #3 from the screenshot below, I'm experimenting right now at a 5ghz 8700K overclock running with HT disabled and all 6 cores overclocked, using the least amount of processor voltage possible, which is BIOS set to 1.250v. This is over 30 minutes of Prime95 and Core Temp readings and CPU-Z. Hope this helps! SS
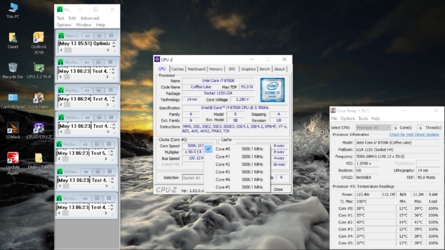
The screenshot was taken at the maximum electrical and wattage load.
Last edited: