- Joined
- Jul 9, 2002
- Location
- Sotira, Cyprus
Hi!
Have done a little bit of researching for my own use so may as well put it here so others, if they wish to do so, can use.
Basically what it came down to was that with a vast range of waterblocks on the market each performing differently on different CPU's, I wanted to know what I could do to make sure my Raystorm waterblock was working as efficiently as possible for my FX-8350 CPU.
So below are my findings.
Firstly, I used two images from the web to get an approximation of a few things (images below).
The next image shows my findings which I will discuss.
OK, firstly, I wanted to know where the cores where in relation to the inlet of my Raystorm block.
As can be seen in the images, the inlet lays right in the middle of the CPU (which we can see is directly above the L3 cache).
So what I will be doing is to create a new inlet plate so that the water will first 'hit' cores 5/6/7 and 8 first, then move other the L3 cache and then finally over the other cores.
When pushing for maximum prime performance it is almost always core 5 and 8 that I have issues with so will find out if my mod will make any sort of difference.
This will be the first step, as alot of us know these FX CPU's are really picky once they go over 62C package temperature.
So anything I can do to keep lower than this can only be good!

Anyhow, will post back when I have some results (wont be for a good week while I wait for a replacement CF5-Z to arrive).
Have done a little bit of researching for my own use so may as well put it here so others, if they wish to do so, can use.
Basically what it came down to was that with a vast range of waterblocks on the market each performing differently on different CPU's, I wanted to know what I could do to make sure my Raystorm waterblock was working as efficiently as possible for my FX-8350 CPU.
So below are my findings.
Firstly, I used two images from the web to get an approximation of a few things (images below).
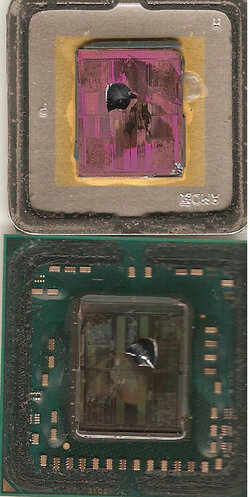
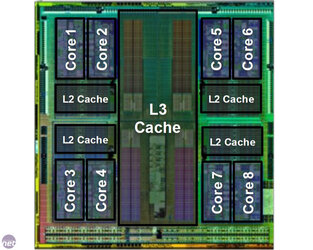
The next image shows my findings which I will discuss.
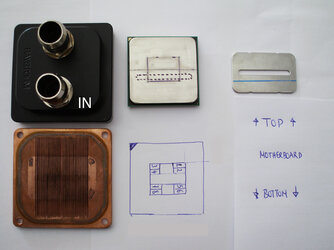
OK, firstly, I wanted to know where the cores where in relation to the inlet of my Raystorm block.
As can be seen in the images, the inlet lays right in the middle of the CPU (which we can see is directly above the L3 cache).
So what I will be doing is to create a new inlet plate so that the water will first 'hit' cores 5/6/7 and 8 first, then move other the L3 cache and then finally over the other cores.
When pushing for maximum prime performance it is almost always core 5 and 8 that I have issues with so will find out if my mod will make any sort of difference.
This will be the first step, as alot of us know these FX CPU's are really picky once they go over 62C package temperature.
So anything I can do to keep lower than this can only be good!
Anyhow, will post back when I have some results (wont be for a good week while I wait for a replacement CF5-Z to arrive).
Last edited: